Basic Oxygen Furnace Automated Tapping System
Share
Legacy Project
Control System Design and Installation
A major steel producer in Hamilton, Ontario had a steelmaking improvement program that consisted of over thirty projects that were completed during a period of three years between 2005 and 2008. These projects involved both steelmaking lines; the Basic Oxygen Furnace (BOF) line and the Electric Arc Furnace (EAF) line. The projects ranged in complexity, size, cost and duration.
The following is a description of the automated tapping system that was installed at the Basic Oxygen Furnace.
Originally, once a batch of molten steel had been prepared in the BOF vessel, the molten steel would be poured or "tapped" from the vessel into a ladle. This process required the manual tilting of the vessel via joystick controls to allow for a maximum steel depth over the tap-hole to maximize the tapping of steel out of the vessel into the awaiting ladle, while minimizing the slag transfer via the tap-hole or over the lip of the vessel mouth. At the same time, the operator would be required to manually adjust the position of the ladle, which was sitting on a transfer car, to ensure the tap stream was centered on the ladle and initiate the additions of flux and alloys to the steel in the ladle as required.
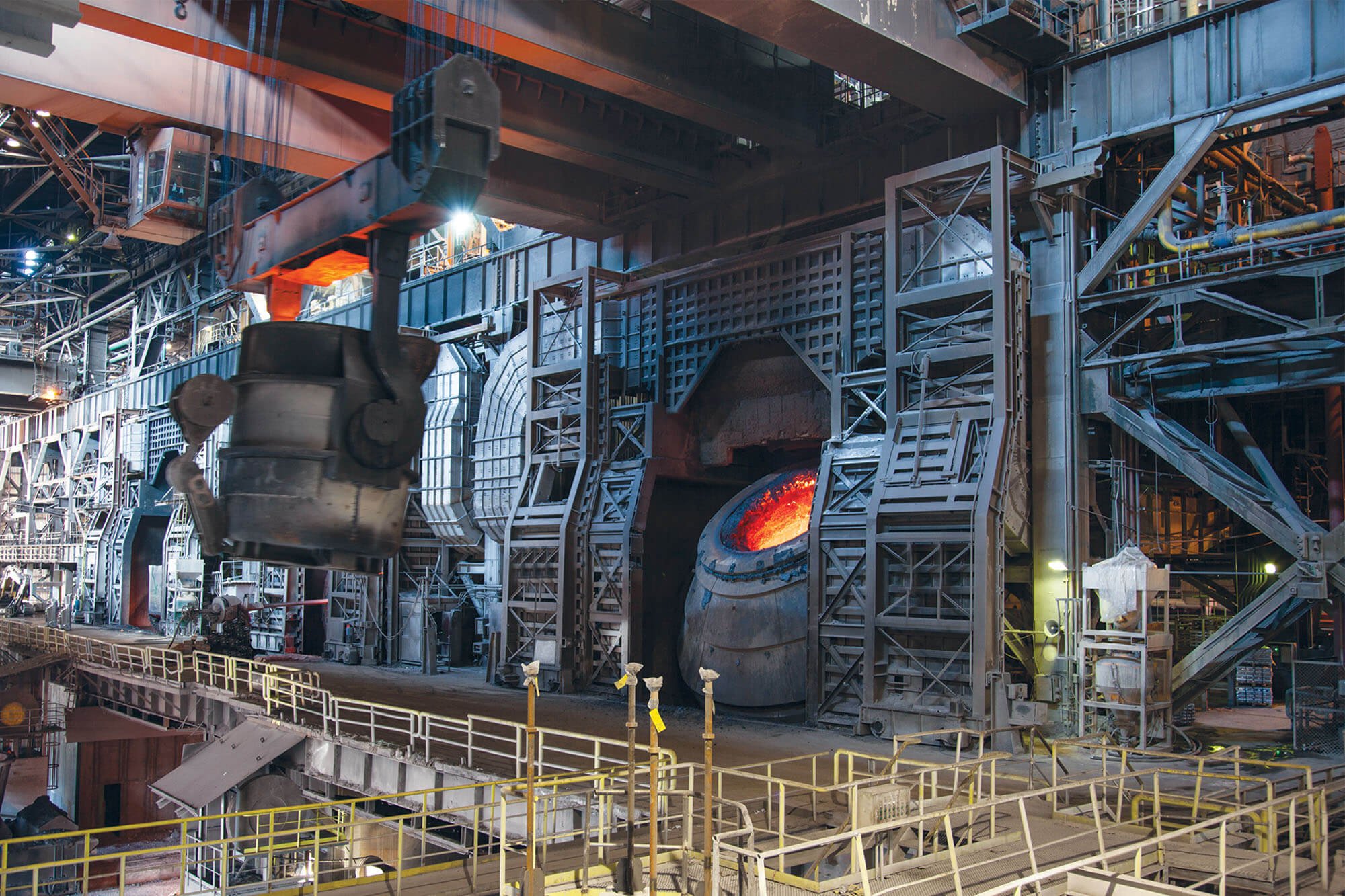
Manual tapping process.
As the steel was tapped out of the vessel, an increase in slag being drained through the tap-hole would be detected by an existing tap stream slag detection system. Once a preset amount of slag was detected in the tap stream, an alarm would sound and the operator would manually tilt the vessel upright, completing the tapping process. The operator would then be required to manually move the ladle and transfer car to the next position via joystick controls. Eventually, the ladle would make its way through the Ladle Metallurgical Facility (LMF) before progressing to the caster.
Prior to tapping however, the ladle must be prepared. Originally, the preparation process was all manually controlled, which included:
- Positioning of the transfer car for loading/unloading, sanding, preheating, tapping, weighing and sampling of the ladles;
- Scale control (weighing/taring of ladles);
- Pre-heater control;
- Sanding of the ladles;
- Sanding verification of the ladles.
Due to the manual operation, the process was inconsistent resulting in variations in steel quality, slag carryover, and process durations.
Taking advantage of the control system upgrades made via projects completed earlier in this program, along with the integration of a ladle sanding verification system developed by the steel producer's process automation group and the integration of the SlagView system developed by Nupro Corporation, the entire BOF ladle preparation/tapping process was automated.
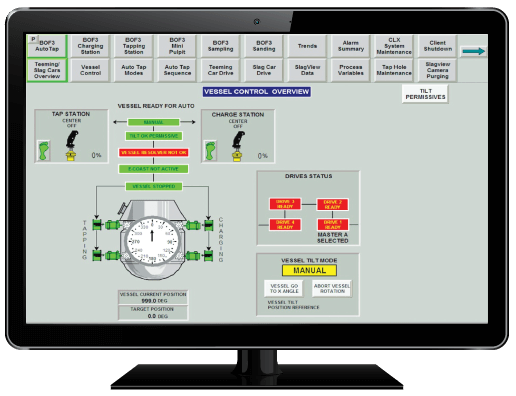
Automated tapping interface.
This was the first BOF facility with automatic tapping capability in North America. In it first year of operation, the auto tapping capability was available for 99% of the taps and was used for more than 90% of the taps completed at the BOF facility. As a result, steel quality has been greatly improved and re-applies (outside of quality standards) have dropped substantially.
JNE Automation's scope of work for this project was a follows:
- Project management;
- Commissioning management;
- Engineering design for the mounting of the SlagView and LSVS hardware;
- Control system design for the integration of the SlagView and LSVS systems;
- Control system design for the automatic control of the pre-heater and ladle additions;
- PLC programming (Rockwell RSLogix software – 4 PLC's);
- Network configuration design and commissioning (Rockwell RSNetworx);
- HMI programming (Rockwell RSViewSE – Redundant servers w/ 2x Thin-client servers w/ 10 Thin-clients);
- Onsite installation support/supervision;
- Onsite commissioning and operator training.
With offices in Hamilton ON, Pittsburgh PA, Livonia MI, and Auburn AL, our experts can help you achieve the industrial automation solutions you need. Contact JNE Automation today.
Control System Design and Installation
A major steel producer in Hamilton, Ontario had a steelmaking improvement program that consisted of over thirty projects that were completed during a period of three years between 2005 and 2008. These projects involved both steelmaking lines; the Basic Oxygen Furnace (BOF) line and the Electric Arc Furnace (EAF) line. The projects ranged in complexity, size, cost and duration.
The following is a description of the automated tapping system that was installed at the Basic Oxygen Furnace.
Originally, once a batch of molten steel had been prepared in the BOF vessel, the molten steel would be poured or "tapped" from the vessel into a ladle. This process required the manual tilting of the vessel via joystick controls to allow for a maximum steel depth over the tap-hole to maximize the tapping of steel out of the vessel into the awaiting ladle, while minimizing the slag transfer via the tap-hole or over the lip of the vessel mouth. At the same time, the operator would be required to manually adjust the position of the ladle, which was sitting on a transfer car, to ensure the tap stream was centered on the ladle and initiate the additions of flux and alloys to the steel in the ladle as required.
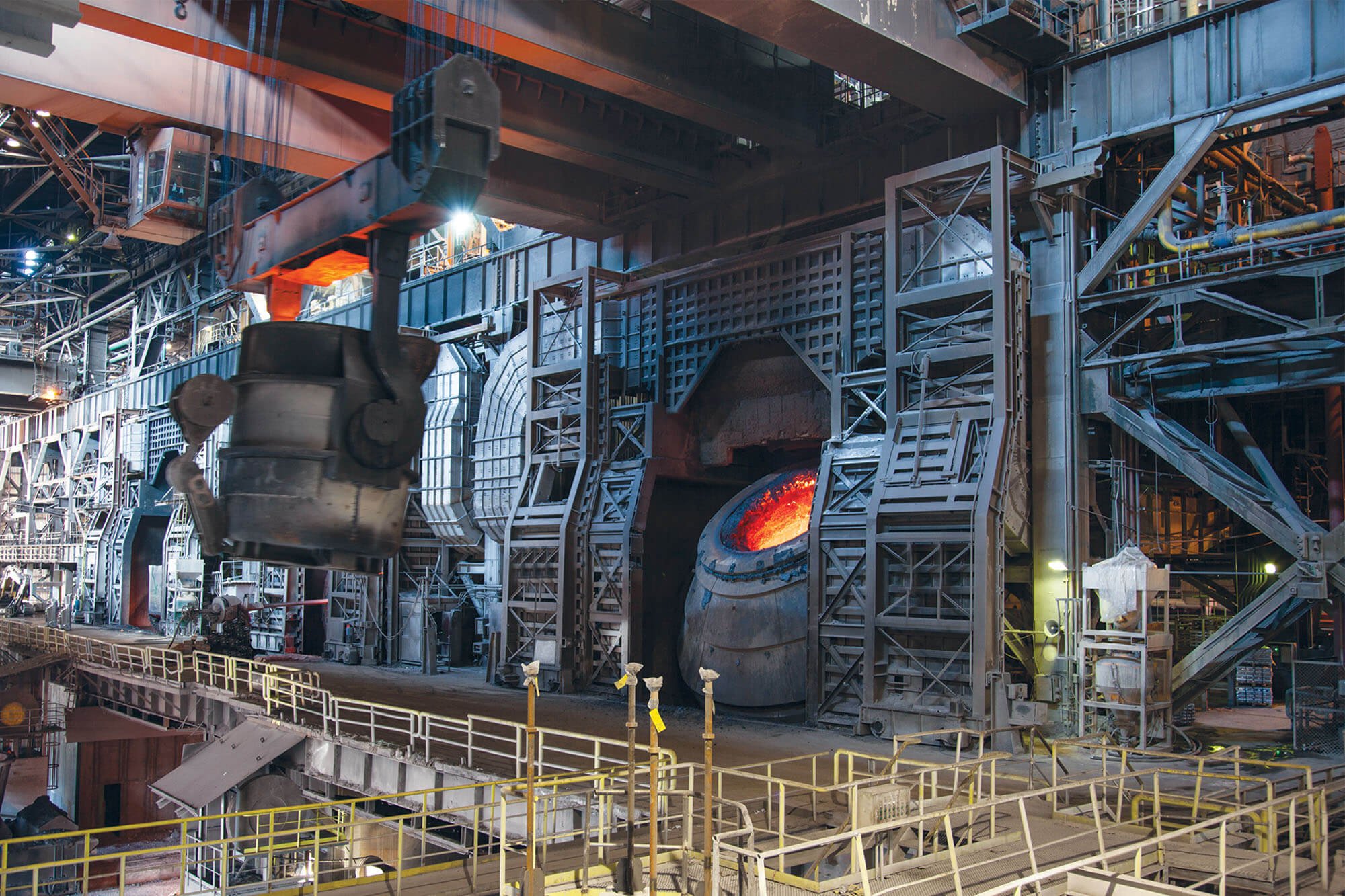
Manual tapping process.
As the steel was tapped out of the vessel, an increase in slag being drained through the tap-hole would be detected by an existing tap stream slag detection system. Once a preset amount of slag was detected in the tap stream, an alarm would sound and the operator would manually tilt the vessel upright, completing the tapping process. The operator would then be required to manually move the ladle and transfer car to the next position via joystick controls. Eventually, the ladle would make its way through the Ladle Metallurgical Facility (LMF) before progressing to the caster.
Prior to tapping however, the ladle must be prepared. Originally, the preparation process was all manually controlled, which included:
- Positioning of the transfer car for loading/unloading, sanding, preheating, tapping, weighing and sampling of the ladles;
- Scale control (weighing/taring of ladles);
- Pre-heater control;
- Sanding of the ladles;
- Sanding verification of the ladles.
Due to the manual operation, the process was inconsistent resulting in variations in steel quality, slag carryover, and process durations.
Taking advantage of the control system upgrades made via projects completed earlier in this program, along with the integration of a ladle sanding verification system developed by the steel producer's process automation group and the integration of the SlagView system developed by Nupro Corporation, the entire BOF ladle preparation/tapping process was automated.
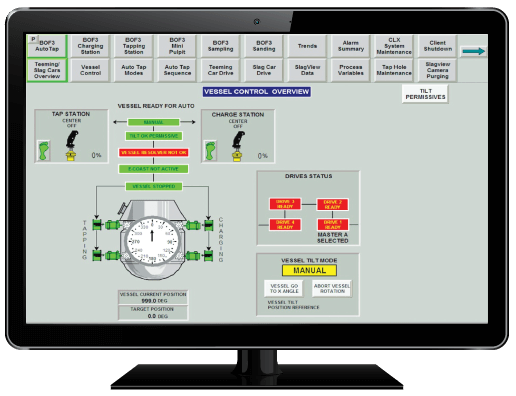
Automated tapping interface.
This was the first BOF facility with automatic tapping capability in North America. In it first year of operation, the auto tapping capability was available for 99% of the taps and was used for more than 90% of the taps completed at the BOF facility. As a result, steel quality has been greatly improved and re-applies (outside of quality standards) have dropped substantially.
JNE Automation's scope of work for this project was a follows:
- Project management;
- Commissioning management;
- Engineering design for the mounting of the SlagView and LSVS hardware;
- Control system design for the integration of the SlagView and LSVS systems;
- Control system design for the automatic control of the pre-heater and ladle additions;
- PLC programming (Rockwell RSLogix software – 4 PLC's);
- Network configuration design and commissioning (Rockwell RSNetworx);
- HMI programming (Rockwell RSViewSE – Redundant servers w/ 2x Thin-client servers w/ 10 Thin-clients);
- Onsite installation support/supervision;
- Onsite commissioning and operator training.
With offices in Hamilton ON, Pittsburgh PA, and Livonia MI, our experts can help you achieve the industrial automation solutions you need. Contact JNE Automation today.
Contact Us
Connect
JNE Automation's control systems engineers specialize in continuous process and safety control systems, modernizing PLC and HMI systems, integrating OEM equipment, and supplying custom control panels. Based in Hamilton, Ontario, Canada, we service clients locally, nationally, and internationally.